Saturday, May 26, 2007
Wednesday, May 16, 2007
Splog update
Well, after one week I recovered 2 freaking mL of MeOH!!!!! I used an IR thermometer and the glycerin temperture was 55C. Either the MeOH came out so slowly it was not condensed or there was just not enough energy to liberate the MeOH. I don't believe this to be a simple distillation/evaporation. The glycerine is very basic and so the MeOH has to "rip" a proton from somewhere in order to leave the solution. If I try this again I'll do it in the lab where I can watch it more closly. Anyway, I just ended up pouring the glycerin into my compost pile. I was just kind of disappointed and that seemed to be the right thing to do at the moment. I am sure I breathed lots of MeOH in the process. On the up side this was worth a try and it was not a total loss. My compost smells really sweat and it's really dark. I am sure you could run the biodiesel reaction in a compost pile since it was so hot. We should give it a try on a small scale the next time we are preparing a reaction.
Wednesday, May 09, 2007
Blog about splog (aka soap log)
We are starting to stock pile glycerine-MeOH waste at our site. So I thought I'd try something cheap and easy. I have been turning my compost heap a lot as of late and noticed how freaking hot it was inside. I thought maybe I could heat the glycerin-MeOH waste and collect the MeOH. So I poured 15 gallons of waste into a drum and connected it via hose to a 5 gallon vented carboy. I thought the MeOH may come off too rapidly and just blow past the carboy or worse yet blow the hoses off and spray my yard with caustic glycerin. Well ........ 3 days latter, nothing!!! The drum is hot the carboy is cool but no MeOH. I found it kind of funny that you could OD on the the MeOH vapors when the glycerin is warm but you can't collect 1 mL when it's 70C. I'm just going to cover the compost with a tarp to generate more heat and leave it for a few more days. Maybe I'll collect some MeOH or have a huge log of glycerin soap in the drum. Imagine taking a bath with a 2 ft x 1 ft cylinder of soap.
Wednesday, January 10, 2007
The Educating of Ricky Bobby
After my Ricky Bobby with the MeOH I thought maybe I need to step back and educate myself on dealing with larger amounts of liquids before I start NASCAR racing.
Yes we pick the coldest days to work, it was about 0 deg C out side!!! So Dave, Miles and myself got out to Corkey's about 9:30 am Tuesday and heated about 120 gallons of oil to 50 C. It took close to 2 hours. But then again everything we do out there takes about two hours. We added two coffee cans of magansol and pumped and stirred for about 30 minutes. One really neat observation was the state of the oil before we started it was very cloudy it also smelled rancid. After the magnasol was dumped in the smell went away very quickly. The final oil was clear and smelled like normal used oil. We tired to filter with no gravity pressure but found this to be really slow so we went to using the liquid's gravity head pressure to filter with a 50 micron sock. After about an hour we had close to 40 gallons. We were all cold and needing to do some "real" work so we called it a day. There's still about 80 gallons in the reactor (the pipes were drained out) that can be heated and filtered when we want more oil.
Now for the good stuff:
I brought a sample of oil into lab, I wanted to do the reaction as close as possible to the conditions we will see at Corky's. The oil titrated it to a very consistent 2.6 meaning we need 4.9 g + 2.6g = 7.5 g KOH/L of oil. This is about average for used oil. For my 0.2 liter I need 1.52 g KOH. I brought 200 mL of oil to 55 C and added 50 mL of MeOH with 1.52g KOH. The temperature dropped to 50C when the room temperature methoxide was added. On a cold day this temperature drop will need to be addressed. Do we warm the MeOH??? I can hear it now, "Help Jesus, Help me Allah, help me Jewish God, help me Tom Cruise!!!" Anyway, the reaction was insulated with bubble wrap, my new toy toy since Dave told me I wrap up in it to stay warm, and left stir for 3 hours. Next, I wanted to try the 5% prewash method lots of folks are using http://www.biodieselcommunity.org/waterprewash/
The crude mixture was transferred to a separatory funnel and allowed to settle for 15 minutes. The bottom glycerin layer was then set aside. A 10 mL (~10%) water wash was performed where about 20 mL of aqueous liquid was collected over 30 minutes. I should have added the water to the crude reaction and then separated but I wanted the glycerin without water for other reasons. The cloudy biodiesel layer was then stirred and air bubbled overnight to remove the MeOH. This morning it was crystal clear!!! I went ahead and added 0.25 g of Magnasol stirred and filtered at room temperature. I ran a 13C NMR and I can say it is >95% pure. I could not see any MeOH or unreacted oil. I can't say it meets ASTM but should be close.
So now we just need to scale up. I have a few more things to do on the small 40 gallon reactor and I will give this a shot. Hopefully we can get a few gallons produced to pay our electricity bill!!!!!
Saturday, December 09, 2006
Big reactor, big reactions
You have to break a few eggs to make an omelet.
I emailed The Shaman this morning to see if he wanted to try and get the big reactor fired up. He emailed me back and said "no", but I was already on my way out to his place. Nice as he is, he didn't say anything when I showed up at his door unannounced and we spent the afternoon learning some good lessons on large-scale biodiesel production.
Lesson #1. Be careful with strong bases. That burning taste in your mouth when you are watching someone measure out KOH, even in a well ventilated room? It's KOH. There is a large fraction of fine powder in granular bases, and if you shine a strong light behind the "rocks" of KOH while you are handling it, you'll see it floating up in the room. Wear a mask. And gloves. And goggles.
Lesson #2. If you see a weak link, potential problem, or something that might break in a system, fix it or change it before doing anything else. Some cheap plastic fittings snapped today and yesterday. The first two times just resulted in mild anger. The third time it resulted in someone getting sprayed with a pressurized methanol/KOH mixture. This person was out of their pants before the methanol got through the cotton, but it was a big eye-opener. Friends, when you're working with 10s and 100s of gallons rather than milliliters and liters, the pressures change, and failures that are minor inconveniences in an appleseed can become big problems.
Lesson #3. Think bad thoughts. When we got the methoxide mix into the big reaction tank, we heard a foomf. Very exciting. Luckily, we had gone thorough a dry run and long walk through of bad situations and what we would do to shut things down and get out of the reaction room safely. And quickly.
Which we did.
It turns out that the methanol was vaporizing fast enough to exceed the capacity of our pressure relief hose. This caused the top of the tank to pop up and hit some of the boards. Not too dangerous, but eye-opening. In general thinking about how to stop leaks, channel spills, and general plotting gloomy scenarios can pay off if things hit the fan, which they did a couple of times in getting this running.
Lesson #4. Make sure there is a dedicated pressure relief valve in every system. Breaking one of the cheapo pump fittings and loosing some methanol just might have saved us from learning this lesson the hard way. We were going to pump from the methoxide mixer (located outside the reactor room) into the tote through an inlet fitting that would have inadverntantly resulted in there being no pressure relief on either system. Now, I'm no chemist, but I'm thinking that boiling 12 gallons of methanol in a closed system that isn't built to take pressure could have ended-up badly. Check for pressure relief. Unscrew something, put an open hose barb in, or buy a cheap pressure relief valve and put it some place where goo can't clog it.
Now, the good news about all of this is that over the past two days we figured out how to use the blademaster to move thick oil when it is cold, heat it, dry it with magnasol, filter it, mix a big batch of methoxide, and react it, and do it safely. This last part because we broke everything that was weak or unsafe.
So, we're ready for big batches. There are some more tricks that we learned that I'll post in the coming days. Despite the snafus, the reactor and methoxide system is awesome, especially the heater and dual pump system. With another take-off valve at its highest point we can use that system to dry oil, separate glycerine--just about anything!
I'll close by voting that we change the Shaman's nickname to Chuck Yeager.
Saturday, June 03, 2006
Titrations-Not as hard as I thought.
Been a while since I posted anything. I am doing a whorkshop for High School teachers this summer so I thought I'd run a few experiments they will perform. We will titrate some WVO, make B100 and determine it's viscosity. So today I let my 9 year girl and 7 year old boy help do the titrations. I had read the ASTM procedure for a titration and was a little intimidated but after thinking about it I saw where it could be made a lot easier. I made a 1g NaOH/L isopropanol (IPA) solution the day before. We added 25 mL of IPA to a 125 mL flask with a stir bar and then added 3 drops of phenolphthalein indicator . We titrated to a faint pink lasting for about 20-30 seconds. So the solvent takes about 0.5 to 0.8 mL of base. We then add 1mL of waste oil from the Dixie Classic Fair (Dave gave me some a while back). We recorded the starting volume and then titrated to the faint pink again. We recorded the ending volume and subtracted to find the amount of solution used. After four duplicate runs we averaged 2.47 +/- 0.03 mL. This translates to using an extra 2.47 g of NaOH per liter of oil. So this oil would need 3.5 + 2.47 = 5.97 g NaOH/liter oil. A rough calculation tells me this is oil is about 15% FFA. Definitly not a hard test to do. I wonder why it took me so long to try it???? Kids loved seeing the color change, of course.
Tuesday, December 13, 2005
UPDATE: Sugar Catalyzed Reaction
We already know the feed stock oil requires 8 to 9g/L of NaOH when used as is. But after pretreatment with the sugar catalyst I regarded it as virgin oil. I used 3.5g/L of NaOH and 25% by volume MeOH. I heated to 65 C for 3 hours under nitrogen. I also used a reflux condenser to stop MeOH loss. I separated the glycerin off and washed three times with dilute HCl. Then a final water wash. I did not see a lot of emulsion unless I used distilled water??? The washed product was heated to 60 C and allowed to cool overnight. The FAME was transparent and light amber in color. I performed a GC analysis and it passed the GC test. So at least on a small scale (10 g oil) the pre-treatment shows promise. I suspose how well this works for a range of FFA levels as well as how scale effects matters remains to be seen.
Now that classes are over I want to try making a few more acid and base heterogeneous catalysis.
Tuesday, November 29, 2005
Sugar Catalyzed Reaction
Recently there has been a lot of buzz by a Japanese group’s solid acid catalyst made from sugar (Nature, vol. 438, p 178, 2005). They reported converting FFA’s to the ethyl esters. This catalysis is special because it is hydrophobic and consists of sheets of fused rings with covalently attached SO3H groups.
Our group decided to make some and see how well it works. Making the catalysis was easy. We took 2 g of sucrose and heated at 400C for 15 hours under nitrogen. The remaining 0.5 g (loss of mass is due to dehydration of the sugars) was ground and heated to 150C in concentrated H2SO4 for 15 hours under nitrogen. After washing and drying, the yield was 0.61g (about a 30% mass return from the starting amount of sucrose)
From reading (Ind. Eng. Chem. Res. 2005, 44, 5353-5363) about solid acid catalyst we saw where most reactions were using 1 to 5% catalyst by weight. Also the WVO we are using is not tremendously high in FFA based on some initial titrations. So the rational for using this catalysis was to convert any FFA’s to the methyl ester in a fashion that would make the subsequent base step much easier. We also wanted to see if this reaction could also be used to convert the oil over to the FAME. This would mean using a large excess of MeOH. Here were the conditions:
12 g WVO
12 g MeOH (100% by weight, large excess to try to push oil over to ester)
0.6 g Cat (5% by weight or about 40 g/L)
Heat at 75 C for 12hours (again long reaction time for the oil to convert)
After heating, the reaction was filtered and the catalyst was washed with 20 mL THF and 20 mL hexanes. Solvent was removed by rotary evaporation. The pale yellow oil was centrifuged for 15 min yielding a small pellet of glycerin. So workup is very easy.
The small amount of glycerin instantly indicated that the most of the oil did NOT convert over to the ester as wished. Using 13C NMR and comparing to authentic samples we could see that the major component was oil with a small (~10% to 15%) amount of FAME. Actually more FAME than I expected so maybe some of the FFA’s were converted over? So it looks like it worked so far.
I suppose the real test will be the behavior of the “pretreated” oil under base conditions? If the FFA’s were indeed converted over to the methyl ester then the base step should be much easier to process. So next is to setup a base catalyzed reaction and see how it behaves.
Monday, November 07, 2005
TOP STORY: WFU Biofuels Project!

Hey all, Check out the article today on our effort in the Winston-Salem Journal. If you can get ahold of the print version, it has a nice graphic about WVO and biodiesel. The article ran front page with a big picture of Jen above the fold. Let's keep up the Big MO!
Monday, October 31, 2005
Molecular Scissors
A guy named Richard Carpenter has recently raised a question about B100 use in modern diesel engines on the Biofuels Interest Group (BIG). His observations have centered on the potential problems of using B100 in modern diesels given the differences in viscosities between B100 and petrol diesel. Here are the viscosities of petrol and B100 at 27 and 75C:
27C 75C
petrol 4.3 1.5 (mm^2/s)
B100 (soy) 11 4.3 (mm^2/s)
So B100 only approaches the viscosity of "cold" petrol diesel when heated to 75C. From what I understand the forces in the injection systems skyrocket given these differences. The fuel is injected at about 22,000 to 26,000 psi!!! In a nutshell, without software changes the engines run less efficiently. There are also increased stresses in the injection pump systems causing some "unconfirmed" premature failures. This does not help B100 acceptance but does create a need to blend.
I started looking for articles that address this problem in B100. I knew ozonlysis of FAME would produce shorter chain esters and that would produce a less viscous fuel. So I search and found this:
A recent paper by Ramani Narayan in Biomacromolecules 2005, 6, 1334-1344 looks at the ozonlysis of FAME. He is Chemical Engineer at Michigan State University. They treated methyl soyate (FAME) with ozone in a process called ozonlysis. The reaction will take double bonds cleave them by either oxidative or reductive pathways. The end result is the production of 9, 6 and 3 carbon chain esters from the UNSATURATED esters. They did not report any viscosities on the ozonized FAME but did report a change in volatilization temp of 135C to 73C (petrol diesel is ~76C). They also reported no change in temperature for the onset of crystallization in region 1 (long chain saturated esters) but a depression in region 2 (unsaturated esters) from -63C to -86C. They did not measure the viscosity of the ozonized product but I wager the numbers are lower.
Since the reaction is cheap and easy I bet we may see more about this. Especially for mono and polyunsaturated B100 derived from oils like Canola, Peanut and Soybean. I also wonder what effect we would see on the ozonlysis of SVO. So if and when we are able to measure viscosity we have some measuring to do.
Tuesday, October 25, 2005
What's coming out of that pipe?
I've been reading a lot of papers on testing and production of B100. I found a very good review article (Analytical Methods Used in the Production and Fuel Quality Assessment of Biodiesel, Transactions of the ASAE, Vol 44(2), 193-200). There are several methods used to monitor fuel quality; Gas, High Performance Liquid and Gel Permeation Chromatography. As well as spectroscopic methods; proton and carbon 13 NMR and Near IR. Other methods are viscometry, titrations and enzymatic reactions.
I was surprised to find that Near IR or Viscometry are the methods of choice for routine evaluation in production. Soy oil has a viscosity of 32.66 mm^2/s at 38C and Soy FAME has a value of 4.41 mm^2/s at 40C. This method is suitable for process-control purposes. So if you are producing B100 and the viscosity changes a lot then you go to GC analysis to figure out what’s wrong. A lot cheaper and faster.
I’ve also been reading about continuous reaction processes. I have many more questions than answers. I’d like to go and tour a B100 plant to see how the big boys do this. I have learned that without some technical advantage then only scale of economy will allow you to be competitive in the market place. Here’s an example of a company that has spun off from CARNEGIE MELLON UNIVERSITY. Full article here: (full article here: http://www.innovations.harvard.edu/news/7954.html )
“Conventional biodiesel plants use batch processing, mixing together alcohol and liquid catalysts that are stirred and heated to produce a methylester from a pure plant oil or animal fat, along with the by-product, glycerine. The processing of pure oils prevents them from thickening too much in colder temperatures.
By contrast, Capital Technologies' equipment and process involves microwave heating, proprietary solid catalysts and continuous processing that can be expanded by adding production modules that the company is assembling at a South Side manufacturing facility, said Marc Portnoff, senior scientist at CMU's Center for Advanced Fuel Technology.
The CMU center developed the new process with financial sponsorship from Capital Technologies, which until recently was a research and development venture backed by investors, including Jackson and John Sununu, former New Hampshire governor and onetime chief of staff during the first Bush administration.
Among the advantages of the new technology are that it takes up less space, in part because of the microwave heating, and can be readily expanded, said Portnoff. He, along with the CMU center's director, David Purta, expects to leave his CMU post to join the new venture in several weeks.
In addition, because it uses solid rather than liquid catalysts, "Our cleaning process [to remove impurities from the biodiesel] is a lot easier," and the manufacturing facility can be much smaller, Portnoff said. Production rates also are double the rates for conventional processes, he added.”
I have found papers reporting FAME synthesis using microwaves and solid catalysis. The technical advantages are faster reaction times (less energy input) and little or no washing. That’s right, little or no washing!!! Now imagine a centrifuge at the end and you have a nice continuous process. So as we build a batch processor I’d like to see someone build a small bench-top continuous processor, sort of a proof of concept project.
Monday, October 17, 2005
DOE
Who says the gov't is lame on alternative energy? At least they make pretty and informative web sites, like this one from DOE. It has a great biofuels section.
Grants
The Sorcerer's Apprentic and I are ready to submit 1-2 Pro Humanitate grants on November 9th and The Educator is working up an EPA curriculum grant. Should we move into the big leauges? Here are a couple of sites with links to grants that I think we might be able to land. From the biology side there are some simple things that we could do with algal stocks and oil degrading organisms that would be competitive, I think. Here is the NREL biofuels site, and there are some great links to grants at the Oak Ridge biofuels site.
Should we make a list of tasks and deadlines to keep the project rolling?
Friday, October 14, 2005
Shaman says: make a hexane still
Yesterday afternoon the Shaman, the Sorcerer's Apprentice, and I were talking about producing BioD from virgin oil rather than waste. Now, we're not looking to upset the apple cart on the plans for the bigger reactor, but we were doing some brainstorming. In particular, we were looking at the economics of making biodiesel from oil that we grow cooperatively with local farmers.
The oil yield per bushel (and per acre) varies a lot among crops, and the ways that oil is extracted varies a lot, from mortar and pestle, to mechanical (ram and screw presses) all the way up to the solvent methods that the big-boys use. Looking at straight oil extraction, it doesn't look like traditional crops are going to be cost effective unless you factor in the profit gained by using the meal. Home-pressed sunflower oil comes out to >$10/gallon, and soybean oil comes out to ~$4.50 a gallon, the latter just figured on yield per acre and the cost that an acre of soybeans can bring. Canola seed and other oil crops might be able to do better, particularly if you can find a way to use the meal (like feeding it to my pigs or cows).
So, where does hexane play into all of this? Well, the Shaman was talking about making a hexane still to extract the oil out of flaked soybeans, or whatever other crop we use. Hexane is cheap, and super flammable (two qualities that endear it to pyros) and also gives a super efficient extraction of the oil. And, the meal can be used afterwards. Hexane in your food, you gasp? Read how the vegetable oil you use is extracted from the bean. What they don't get goes into your textured soy protein and animal feed.
Other sources of oil that the Shaman came up with were looking for vegetable oil that passed its expiration date, and also trying to find an oil processing plant somewhere around here and trying to get the tails of the batches that they can't sell for food.
So, friends, keep your noses to the ground for sources of oil. Also, Oily SOB, it might be time to contact your big batch waste producers and to try and tap into the big streams of waste oil. The amount of effort we go to to collect small batches probably will end up costing more than just heading out to buy regular diesel. While it is still nice to run biodiesel in terms of being carbon neutral, helping farmers, and sticking it to the terrorists and The Man, it sure would be nice to make it pay too!
Thursday, October 13, 2005
What does a raw soy bean taste like anyway?
I was talking to my farmer friend this morning about growing soy beans and what happens to them. I found out where they have them ground and then sold to a broker. He promptly walks over to big hopper and with one hand (equaling all muscle tissue in my entire body) and scoops out a bucket full of soy beans. He then picks a bean out and pops it in his mouth and commenced to chewing!! Not to be out done, I too picked up a bean and starting chewing and chewing and chewing. Tasted like...... uhhh, uhhh...chicken. No not really. It tasted like a raw peanut. I have about 15 to 20 lbs of soy beans (dried from last year) in my office if anyone wants to play with them.
I thought a pretty cool lab exercise would be extracting the oil from a known weight of beans. Could then try other beans to see the difference. I suppose if you are buying beans for the oil you could evaluate the beans based on oil yields rather than just bulk mass. Probably the next week's lab would then be making biod from the extracted oil, right?
Salem Hall room 9b if you want some beans otherwise, I'll give the left overs to B. and A. King (chem profs), they have chickens and goats. A goat will eat anything right?
Tuesday, October 04, 2005
Tank Report
I washed the remaining resin out of the big tank with pressurized gasoline. It worked quite nicely. We have something to start the next bonfire with as well. I found more on the tank contents and it can have up to 50 ml/L in potable water, so I imagine it isn't too nasty.
The next tanks that we're getting from the super-donor contained Silastol PHP 26, which is a finishing agent for fabric fibers. The MSDS looks benign, and it is fully miscible with water, which is a definite plus. Translation: awesome!
Oil update

Just back from checking the bins at the Dixie Classic Fair. We had a bit of a SNAFU this morning as I hadn't gotten all the ammonium resin out of the big tank. We dropped off some extra oil collection tanks, so everything should be okay as far as our responsibilities to collect oil.
After getting back, I took the tank over to the Chemistry department and the Shaman and I tried to figure out how to clean the tank goo out. It looks a bit more difficult than expected. Soap doesn't touch it, acetone, methanol and ethanol don't do too well with it, and toluene is marginal. Petroleum ether does a good job, as does cooking oil, so we thought that gasoline might be the best solvent. We'll give that a try this afternoon. It might be good to pressure wash the tank as well. I've ordered the MSDS sheet and will take a look. As we're going to be getting 20 of these big tanks, we'll need to find some easy way to deal with the contents!
Sunday, September 11, 2005
Captain Dave & Co.'s First Batch--Ideas?

Over the weekend we took a shot a making some fuel. Some things went well. The plumbing behaved as it was supposed to for the most part, or at least could be tweaked to do so. One problem, though, was the water heater, which didn't really heat much on Saturday. The attempt on Saturday resulted in no separation of fuel and glycerine, which might have been attributable to the low temp. So on Sunday we tried again, this time after getting the heat on. Our thermometer indicated that the temp got only to 120 F. We need to calibrate this thermometer and see if it is accurate. Assuming that it is, it was a mystery to me why we leveled off at 120 when I had the setting cranked to 130 and then 140 (Paul?). In any case, 120 seems close to 130 and Steve thought that as long as the oil was liquid that the difference between 120 and 130 was not a problem.
So, we're at 120, and I ran the circulating pump for about 90 minutes of reaction at 120 F. Except, looks like no reaction took place. I gave it all day to settle, and no separation occurred. It looks now the same as when we first mixed the methoxide with the oil on Saturday afternoon.
This evening I took some of the reaction mixture to the lab and got a pH, with a stir bar mixing well 1 ml of the reaction mixture in 10 ml of isopropanol. pH was 9.86! I was concerned that the mixture was still too acidic, because the sodium methoxide that we mixed with the oil on Saturday was made as 150 g Red Devil lye in 10 liters of methanol added to 50 liters of oil (3 g lye/liter of oil). This is at the low end of the lye concentrations that you find in recipes. Instead, the reaction mixture is quite basic. We need ideas on how it got to be so basic (something that had been in the water heater?), and how to get it into the desired 7-8 range.
Notes:
-I flushed the used water heater with tap water for about half an hour last week, and got a lot of sediment to drain out. When I was done, it seemed like nothing else was in there, but who knows.
-I have a sample of the original oil and of the current reaction mixture, in my lab. Marcus and Jen, would you like to have a go at them and see what you think they are made of?
-when the thermometer says 120 F, the pipes are pretty warm. I wouldn't want to take a bath at that temperature. So, I suspect that the thermometer is not far off.
Wednesday, September 07, 2005
The latest haul
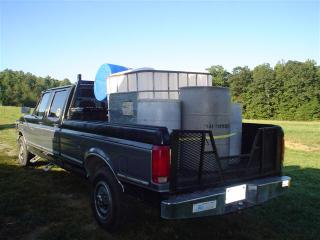
Last night Robert and I drove the back-roads of Guilford County in search of tanks and oil. This is the load that came home in the beast. We're up to a couple hundred gallons of oil, a half dozen barrels, a 300 gal. wash tank. I think it is time to get some product out! Also, Paul went to his Yadkin County junk yard and found two 60-80 gallon stainless-steel soup tureens. They have water jackets, so they just might be the ticket for hooking up to a solar panel.